In-Line Gauge Control
Welded Tube Pros experience in strip
handling & storage for welded tube, pipe, cold roll forming and stamping processes are now married
with I²S (Integrated Industrial Systems) capabilities to provide the best possible patented in-line gauge and
camber controls for today’s high speed, high precision, welded tube, roll
forming, and stamping lines.
In-Line Gauge Control offers the welded tube
producer a process to consistently reduce conversion losses, improve
profitability, and produce superior tubular products with potential sales
opportunities in new markets without extensive capital investments. The
application of the process to Welded Tube production is not limited, by
materials, by weld speed or by material thickness.
In-line control permits the use of the widest possible raw material
sources (steel chemistry and basic physical quality must be similar), thereby
permitting further flexibility in raw material purchasing. The process
offers, in some instances, further savings by permitting substitution of
alternate materials, for example HRS P&O for Cold Rolled.
In-Line Gauge Control offers tube producers the ability to be more
competitive and less dependent on their steel suppliers.
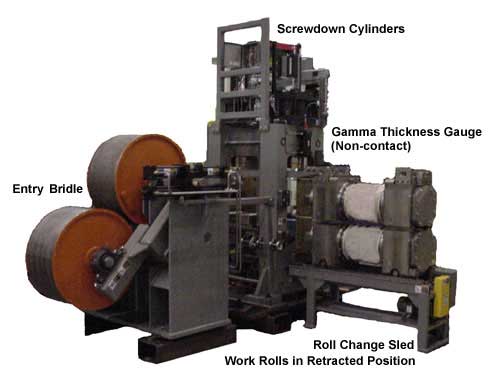
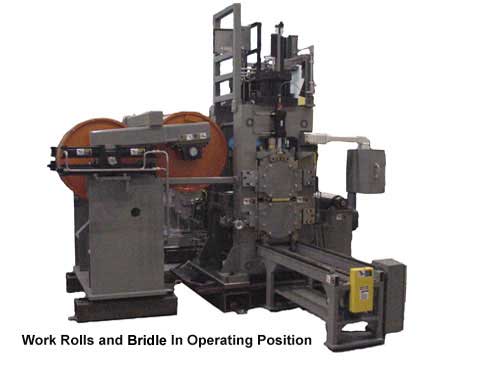
Tube
Production Objectives through the Application of In-Line Gauge Control
Provide
Reactive Control of Tube Wall in ERW Tube Production. Give the operator the ability to CHANGE the incoming gauge and correct
camber conditions. Permit Consistent Production of HIGH QUALITY Tube Products.
The operation that does not provide quality products will be gone! Provide the capability to use Alternative raw materials.
Upgrade hot rolled gauge tolerances so it can be substituted for cold rolled,
where surface finish is not a requirement.
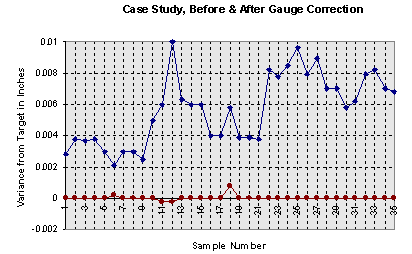
The chart above shows a recap of actual measured thickness readings before and after gauge correction.
The upper graph depicts variation of the strip prior to gauge correction.
The lower graph shows the result of gauge correction.
Before Correction:
Average 0.0056", Range 0.0075" , Stand. Dev. 0.0021, Cp 0.1551, CpK -0.8676
After Correction:
Average 0.00001", Range 0.0010", Stand. Dev. 0.0001, Cp 2.2880, CpK 2.2880
Reduce
raw material cost.
Upgrade HRS P/O gauge tolerance so it can be substituted for cold rolled where
surface concerns are an issue. Upgrade low carbon steel to the strength requirements of a higher carbon or a
medium carbon to that of HSLA.
Reduce
Production Cost, Increase Profits.
Maximize utilization of the available personnel skills and raw
material! Reduce waste. Maintain labor cost while Increasing
production. Increase profits.
What
is In-Line Gauge Control?
An
operator controllable process to maintain material thickness entering the
tube mill. With non-contact thickness measurement at the exit of the tube mill,
a closed loop control can automatically adjust entry strip thickness. A self-correcting thickness control that adjusts for both variations in
strip thickness and hardness once set by the operator. An automatic process that can also reduce strip camber problems while
correcting thickness variation.
Why
Use Gauge Control?
Reduce
roll wear and reduce set up time by providing uniform strip thickness with
reduced camber variation. Permit purchase of commercial grades in lieu of close thickness tolerance.
Permit substitution of material grades. Actively make Tube Walls to +/- 0.0005" of desired wall.
The process converts over gauge material to thinner and longer sections. On
strip widths common to small tube production, the vast majority of material
growth is to length, with normal reductions being 10% or less. Below is
shown a rolling study performed on 6" X 0.257" thick, low carbon, hot
rolled. The width growth for a reduction of 8% would be on the order of + 0.1 to
0.2%. As strip width increases the growth in width decreases.
The
experience of I²S
I²S
has the largest engineering staff of all U.S. mill builders. With over 1000
years (combined) of experience in the mill industry, our employees have worked
for the following mill companies: Sendzimir, Waterbury Farrel, Fenn, Ruesch,
Loewy, Fagersta Steel (Sweden), Salem Stainless Steel (India), Ulbrich Stainless
Steel, Chase Brass, American Brass, Scovill Brass, Century Brass, Stanley Steel,
Torin Company, Cold Metal Products, Superior Steel, HMSS Sczopience (Polish
Brass), Republic Steel, SMS, Wean, and Tippins Machinery.
Over
30% of our staff is engineering. Our engineering staff is comprised of
professionals specializing in software, electrical, mechanical, hydraulic,
coolant and structural design. Equipped with some forty CAD stations, which are
networked together, each engineer, designer and drafts person has a precision
drawing tool in their hands. Access to all the drawings for a given project is
provided by our Windows NT based computer network. This facilitates precision
engineering and ensures the accurate implementation of design changes on each
project.
Mechanical engineering personnel are grouped by equipment categories to allow
them to exchange knowledge and operate efficiently in a single area. The project
leader is fully supported by members of specific groups which focus on designing
and detailing of systems such as hydraulics or coolant. Members from all of
these areas join to form a team for the duration of each project.
A team of two electrical engineers (project coordinator & backup) is
assigned to each project. This combining of experience and talent results in
continually improving designs and innovations to increase productivity and
safety on our mills.
Each I²S mill is custom designed around your needs. In the design process we
employ the newest computerized geometric element analysis (GEA) technology.
Solid modeling is used to make accurate predictions in mill components such as:
mill housings, winder shafts, rolls, etc.. GEA allows exact geometries to be
modeled accurately. The data derived from the analysis enables the engineer to
identify critical areas of the part and compensate in the design to achieve the
acceptable stress and deflection values for its application. I²S engineering
means quality equipment designed for longevity and safety.
For
more information - CONTACT US
Please
view the articles below:
In-Line
Gauge Control in Welded Tube Production - By W.B. 'Bud' Graham From
the Tube and Pipe Journal, July 2001. Equipping
a Modern Tube Mill Part 1 - By W.B. 'Bud' Graham From
the Tube and Pipe Journal, July & August 2001. Equipping
a Modern Tube Mill Part 2 - By W.B. 'Bud' Graham From
the Tube and Pipe Journal, September 2001.
Articles
to download: These are Adobe PDF files. For
a free copy of Adobe Acrobat Reader, click below.
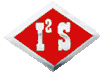
HOME
MAIN SITE MAP CONTACT
US
|